Rubin
Server room
FREE COOLING
ABOUT
Energysaving free-cooling system for server rooms, data centers and other technological areas.
The device is built up of independent modules, which allows for flexible use and economic implementation. We can offer suitable configurations for various needs. Whenever local conditions permit, the device provides steady room temperature by fan-driven ventilation. If needed, the unit defrosts the system using the heating operating mode of AC units or radiator heating. The equipment can directly control the compressor or internal and external fans of traditional climate controller systems without the need to install a winterizing set. It manages heating and cooling air conditioners in both operating modes. Due to its configurable alarm values, it can send a warning about any issue before the event actually occurs.
Compatible with any climate control device
Always provides appropriate cooling
Replaces ‘winterization’ maintenance
Intelligent controlling and management
Lowers the number of maintenance operations
Lowers the risk of failures
Recommended
We recommend this service to Companies and providers where the datacenter has a key function in the process and need low PUE. Careful planning and coordinated work of various specialties are needed to design and successfully operate the system. In addition to providing the appropriate hardware equipment, we design the control unit, visit the location and assess it from a mechanical engineering aspect, and then design and implement the system.
TECHNOLOGY
We economically combine the benefits of air-conditioning and ventilation systems while using an alternative method.
Rubin COOL
Energy use and climate control
Demand for comfort has increased at homes and industrial facilities over the past decades. This inevitably led to the need of climate control almost everywhere. The trend is clearly indicated by the fact that power consumption during the summer months is higher than in the winter, primarily due to the large number of air conditioning units operated in an unplanned manner.
At the same time, recent years have seen revolutionary development in information technology and communications resulting in more and larger server rooms, base stations and data centers. Expectations regarding temperature control differ significantly. There is an interesting difference in.
The figures indicate that the majority of the energy consumed by the residential sector is heat (heating, hot water) while electricity is the main energy source for the IT sector. In general, greater savings can be realized where base consumption is higher. Therefore, any innovative solution designed to lower industrial electricity consumption or residential demand for heat is destined to succeed.
This is especially true for areas with a high number of air conditioners as they also use electricity. Data collected from the European communication industry indicate that this amounts to 30–48% of all the energy used depending on how modern the systems are. Air conditioners are basically designed to cool down the generated internal heat and the heat received from outside in a way to create a balance in a preset temperature range (with different values for comfort and technologies). Almost all of the electricity used in computer rooms is transformed into heat depending on the number of bits traveling. This heat needs to be cooled down using air conditioners. In theory, compressor type air conditioning units have a power efficiency (used to convert electricity to heat energy) of 30%. This parameter is described by the so-called COP value, which is 3 in this case. Metered EU data in the IT sector show only 2.1, which leaves lots of opportunities for saving. Especially when you use an innovative solution that can increase this value by an order of magnitude.
You have different requirements for the temperature control of a home and for an IT computer room. Requirements are summarized along the key parameters in the following table.
Home | IT room | |
---|---|---|
Use of power | 2-10 kW | Column 3 Value |
Annual maintenance | 1 | Column 3 Value 2 |
Temperature Control | 20-23 °C | Column 3 Value 3 |
Setting time | 1-2 min | Column 3 Value 4 |
Programming by periods | necessary | necessary |
Normal temperature difference | 1-2 °C | 15 °C |
Availability | not critical | 24 h |
Internal heat load | no | yes |
External heat load | yes | small |
Remote monitoring | not necessary | necessary |
Noise sensitivity | large | no |
Airflow sensitivity | large | no |
As you can see, the specific applications require devices that operate differently. This issue is managed by the air conditioner manufacturers on the market by developing a few basic types, then scaling them by performance and then matching each typical user behavior with a slightly configurable basic program for each product family. If users want to make changes in the manufacturer’s programming, they can only do so to a small degree.
Accelerated technological development, in the meantime, has created an interesting anomaly:
Whereas certain technological services become obsolete in the IT or in the communications industry and replaced by new ones within 3–5 years, the infrastructural devices serving these systems, including air conditioners, have life cycles of 8–15 years. Therefore, they can support multiple generations of technological services.
The same is true for air conditioners installed for offices or homes. Each investment is calculated with 10–20 years of operation. A change in use or significant increase in energy prices (which is expected) is hard to manage in a system of fixed installation.
In other words, users are forced to make decisions quite frequently:
- It means replacement of air conditioning equipment to more modern ones or to those more suitable for the changed needs.
- Temporary or permanent turning off of certain machines.
- Reprogramming of existing air conditioners by manufacturers.
- Smart addition to existing machines by external control, adaptation to the specific user’s needs.
The decision has multiple consequences:
- There is an investment cost included. Throwing away fundamentally serviceable, good machines is not economical just because there is a more modern product available on the market.
- There is an increase in operating costs.
- Manufacturers do not like servicing individual needs and other interventions may generate disputes over warranty and operation.
- External control allows for a very flexible system while keeping existing equipment. Programming that meets specific and changing needs can be ensured in the long run. The involvement of air engineering can result in significantly lower operating costs.
Operational safety
Reliable, 24/7 operation is especially important for machine rooms, data centers, IT server rooms and communication networks. This is true not only for basic operation but also for temperature control and power supply. Therefore, each machine room has large-capacity batteries in the same room or in an adjacent room to bypass any power outages. In Hungary these power outages have occurred in the following way recently.
As seen above, power outages lasting longer than 1 hour may reach into the hundreds, which means absolute service outage unless proper actions are taken as computer room running only on battery would overheat as the air conditioners do not work without mains electricity. Most operators prevent this from happening by sending a person on site who opens the door/window to ventilate the room until power supply is restored and the room cools down. This is a costly procedure with uncertain and questionable results.These power outages may cause additional problems. Manual intervention only begins when high temperature is detected. Due to large masses, this high temperature persists for an extended period of time even after ventilation begins. Expensive and sensitive batteries especially require stable indoor temperature. In the event of a power outage, these batteries suffer a heat shock that reduces their reliability and service life.
The service life and capacity of batteries are very sensitive to ambient temperature. A few heat shocks of 30–50 °C can reduce their capacities and ruin their internal structures.
This is particularly damaging because this phenomenon is not visible immediately but rather causes a sudden loss of charge at a later time. Under those conditions they cannot bypass the mains power outage and the system they are designed to support comes to a halt. In terms of costs, the situation is even more dramatic. These batteries are very expensive and thus it is important to keep them working for their full life cycle (8–10 years) instead of having to scrap them after 3–4 years.
Such heat waves be easily develop in stations when the power service stops. Under those circumstances, the integrated air conditioners do not work because their operation requires mains electricity. The heat generated by the technology increases indoor temperature to a critical level of 40–50 °C resulting in devices shutting down (using their integrated protection) and then the service stops. The computer room would also stop if the period of power outage exceeds the period that batteries can bypass. In such cases Diesel generators provide auxiliary power, which, however, may need 15–20 minutes before they can actually be used. If that period is not bypassed by the batteries, the whole system comes to a halt.
The path to solution
Based on the issue presented and outlined, we can point out those key criteria parameters along which an innovative cooling system different from mainstream solutions and matching the primary interests of the user can be designed. Key characteristics:
- Independent from the device type and make. It does not disrupt the internal system of air conditioners.
- It can be used on existing systems.
- It is energy-efficient, lowers energy use and CO emission.
- It is cost-effective, requires no major investment and its return on investment period is under 3 years.
- Operating safety increases because there is cooling even during power outages, which protects technological equipment.
- It can be programmed and reprogrammed in a flexible way to meet the needs for use and to always find optimum working points.
- It can be used to meet industrial, office and home comfort needs.
- It is environment-friendly and lowers outdoor noise pollution.
- It increases the lifetime of air conditioners and lowers their maintenance costs
Practical solutions among European communication companies
First off, we are sorry to conclude that each and every European IT service provider manages the development of technology cooling solutions and comfort level office cooling separately. This may be due to the fact that the two systems have significantly different targets, needs and safety requirements. This separation then leads to a situation when the big leap called “innovation” cannot happen.
Almost all businesses focus on technological cooling (which uses more energy).
Telecom Italia EFFC system. With a top exhaust system it creates a depression space where the filtered fresh air is forced to flow into the room. In small rooms the annual COP is around 50.
Belgacom The air-conditoned cooling system is assisted by a fresh-air cooling system working with 10 °C heat step under 18 °C of outdoor temperature.
Swisscom Mistral system. A simple, fresh air solution with its own data concentrator without a programmable controller. Using this system increases COP above 20.
Deutsche Telekom The DeltaClima system has been developed by Weiss. It uses a central water coolant systems. It mixes outdoor and cooled air using a bypass valve.
These solutions provide various implementations of fresh air solutions but in terms of system technology, providers fail to manage these solutions with existing air conditioners, air treatment units, heating equipment, management systems, access control and safety elements. They do not prepare daily, weekly or other kind of time schedules, they do not have self-adaptation capabilities and do not connect multiple computer rooms with multiple air conditioning units.
The so-called “fresh air” air conditioning units widely used in Hungarian contain, in a single factory-built equipment, compressor and fresh air cooling options. One of the main faults of the system is that it does not flush the space to be cooled with fresh air (one-sided layout), its operation is fixed and instead of space it focuses on equipment. No significant amount of energy is saved and requires careful and costly operation.
One of the easy-to-measure parameters of energy saving is the ratio of compressor and fresh air modes. While the compressor mode consumes 1–5 kW of power, the fan driven fresh air cooling system takes only 0.1–0.3 kW. This is where you can realize your savings.
What determines when you can switch from one mode to the next is best characterized by the heat step value needed between indoor and outdoor temperatures. For the systems described above, this value is between 10–13 °C. It means that if you want to stabilize the temperature of the computer room between 25–30 °C, the ventilation based system only works with outdoor temperatures between 12–20 °C. If the outdoor temperature is above that level, the compressor mode is needed.
The figure below can identify periods when the temperature is suitable for fresh air cooling. Where outdoor temperature (red curve) falls below the blue and green lines, you can operate ventilation with a good coefficient of performance. This is why this heat step is a key characteristic of such a system. This is what professionals call the ∆t value. The innovative solution of Rubin Inc. reaches a ∆t value of 7 °C, which guarantees energy saving ventilation applicable 8 months of the year and by using the nigh periods of the summer months, it can reduce energy use by 80%.
The implemented development project – an introduction to Rubin COOL
In Europe as well as in Hungary, most of the year has outdoor temperatures below the required indoor stable temperature range (20–25 °C). Therefore, the outdoor temperature has a virtually unlimited capacity to reduce the harmful heat generated. Another advantage of such a system is that the “dry air” effect so dangerous for enclosed cooling systems, when the specific heat of the dry air is reduced so much that it cannot extract heat, does not occur here.
The diagram indicates that stable extraction of 5 kW of heat power can be done with a fan that has an opening of only 280×280 mm, an air delivery capacity of 1,920 m3/h and requires only 105 W of electric power and all that only from 48 V DC voltage, which allows the implementation of this operating mode even in the event of a mains power outage.
Fan-based ventilation has been installed at a number of locations in Hungary. Experiences were very positive but it also turned out that a control unit is needed between the air conditioner and the ventilation system that optimizes operation along a target function and controls switching between the two types of cooling. We have also experienced that during high daytime temperatures of the summer season a temperature difference of 6–10 °C cannot be realized and the installed air conditioners begin to work during the day. Overall, lasting ventilation is only an option below 15–18 °C of outdoor temperature; a mixed mode operation is likely for higher temperatures. Since the distribution of the average temperature in Hungary is around 15 °C, we expected that the fan-based cooling system is a viable solution.
Our expectations were proven right by the large ventilation systems installed and put into operation later. Our meter readings and the successful operation of hundreds of stations prove that this energy-saving cooling system can be used all-year round except for two winter months.
In order to maximize savings and cooling accuracy, the developed solution had to be connected to a system and equipped with intelligence. This is why a control unit was added to the device. The knowledge of cooling technology professionals, our past experience and the expected operating parameters and processes between various modes were programmed into a special purpose software that can be modified and improved later to by programming.
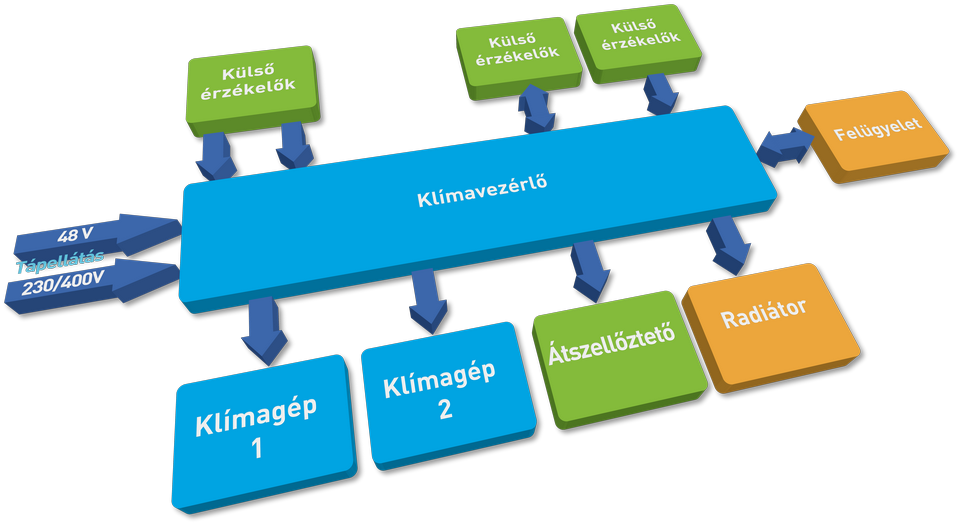
System components:
Existing air conditioning equipment 1 or 2 units, 230 V AC operating mode or 3×400 V AC operating mode
Fan ventilating unit (48 V DC operating mode, with controlled revolution and opening shutters, air filters)
The microprocessor equipped control unitoptimizes operation and reports to network management. It also monitors and handles trouble tickets and supports remote operation. The hardware can be of different in design: Separate heavy current unit (connection, phase switch) and DC operated software controlled electronics. The current SW version allows for continuous functional development and adaptation to new systems. The key functions of the controller are as follows:
- Controls air conditioning units
- Controls the ventilation system
- Controls the heating system
- Maintains connection with network management
- Receives and analyzes sensor signals.
Phase shifter:
A common fault condition for air conditioners with only one current phase is that one of the three phases of the electricity provider is interrupted. In an unfortunate scenario the air conditioner stops even though the station still has two more phases ready to use. For this reason, the control unit has an optional phase switch electronics module that always selects the operating phase to avoid the air conditioner stop working. For 3-phase machines this module is not used.
Our innovation economically implements the alternating use of air conditioning and ventilation based cooling. In the meantime we leverage and optimize the benefits of both cooling methods. We have developed a control unit for the system that monitors outdoor and indoor temperatures, the factory parameters of air conditioning and ventilation and controls equipment to reach optimum container temperature and economic operation. This controller incorporates human professional experience and advancement options in the installed software.
The controller unit provides the opportunity to remotely monitor the operated air conditioners and ventilation systems, as a result of which all main operating parameters and any faults may be monitored and evaluated through a central management system. This will allow to complete most of the configuration and troubleshooting tasks in remote mode thereby reducing human resource expenses as well as dispatch time and cost. At the same time, data analysis allows for system development and optimizations. As a result, the currently running software version has a number of new functions, services and more efficient modes (e.g. adjustment of the rpm of the ventilation fan, standard settings, etc.).
The software control of the system is open and can be used to define any type of operation. As a result, the system automatically switches over to emergency ventilation mode in the event of a power outage, which guarantees uninterrupted operation of the station even in the summer heat. Most of the year the ventilation system works instead of the air conditioner resulting in high savings, reducing the operating period of the air conditioning units thereby increasing their service life and lowering their maintenance costs.
Scheduling of implementation, metering results
Based on the data of the successfully operating equipment, we have calculated total cost of investment, economic efficiency and return on investment.
Operating data revealed that significant savings can be realized in terms of the service life of the air conditioning units and by lowering maintenance and repair costs. As shown on the figure below, this is indicated in advance by the reducing number of switchings and lower overall operating hours.
We regularly metered operating time and power consumption during operation. Based on those, we can conclude that the savings exceed those expected. This is primarily due to the fine-tuned software and that ventilation worked even during the evening and night hours of hot summer days. We had not calculated with that factor in the planning phase.
Technical and economic indicators of RUBIN COOL
The efficiency of the cooling system developed during the innovation can be measured in terms of the following parameters:
Reduced active operating time of air conditioners | 40-75% |
Reduced switching number of air conditioners | 70-90% |
Fewer maintenance events of air conditioners | 30% |
Fewer breakdowns of air conditioners | 45% |
Annual savings on operating costs | 15-20 MHUF |
Annual savings on energy costs | 135-200M HUF (20-30%) |
Return on investment | 2.5-3 years |
Actual savings, of course, depend on outdoor temperature. The Hungarian average temperature and the optimum operation level of the system almost overlap at around 18 °C. Therefore, energy savings can be maximized as indicated by the metering data aggregated based on the actual operation of hundreds of installed systems.
The data of the diagram indicates that our expectations have been met by an annual energy saving of 20,000 kWh resulting in a saving of 700,000 HUF/day. It is clear that the level of saving changes with outdoor temperature.
Unexpected, additional benefits
- The emergency ventilation system is effective even in 30 °C summer heat and the operating ventilation works even during the summer months.
- In the event of an air conditioner fault, there is more time left before the station heats up.
- The service life of air conditioner units increase significantly (5–8 years) thereby increasing future savings on investment.
- Early fault diagnosis is supported by detection of changing operating parameters before breakdown.
- Remote mode in parameterizing, software updating and ventilation.
- The cause of the fault, even if hidden, can be uncovered from stored operating conditions.
Additional opportunities for application
- Operation of inverter air conditioners
- Operation of systems composed of multiple units and rooms
- Operation of comfort systems
Connection to other systems
- Remote management systems
- Security systems
- Comfort systems
RUBICON
Implementation in Biatorbágy
Description of the building
The building has 4 rooms to be cooled, each room has a different floor area and the amount of heat generated in each room is different.
An air-conditioning room was created in the building, where 3 air-cooling units of 30,000 W were installed. These units are also suitable for uncooled air transport. All three devices work in a common air duct, i.e. they are connected in parallel. For this reason, equipment that is not in operation should be separated from that which is in operation by shutters to prevent the return of useless air.
The rooms to be cooled are connected to the common extraction duct by a different number of closing/opening shutter systems:
- Room 1 9 ducts with louvres connected in 3 control groups (2, 3 and 4)
- Room 2 2 ducts with 2 louvres connected in 2 control groups (1, 1)
- Room 3 2 air ducts with 2 control groups (1 each, 1 each)
- Room 4 4 air ducts in 3 control groups (1, 1, 2)
The rooms to be cooled are connected to the inlet duct by inlets with the same cross-section as above, but permanently open.
The intake duct is connected to the air conditioner supply duct with an open shutter in the case of active (compressor) cooling, while the two free air windows of this duct are separated from the outside air by a closed shutter. The inlet channel is then overpressurised.
When ventilated, the intake duct is separated from the air conditioner supply duct by a closed shutter and the warm air exhausted from the rooms is discharged to the outside. The two windows of the air intake duct opening to the free air are connected to the outside air by an open shutter. In the intake duct, in this plant, there is a vacuum, which causes the cool air outside to flow into the rooms in proportion to the amount of air extracted from the rooms.
With ventilation, the rate of air exchange in the rooms is much lower than with active cooling with the same number of chillers. This reduction is caused by vacuum intake and the choking of air filters that clean the outside air.
If the control needs to increase the airflow of cooling air in the common air ducts, this can be achieved by switching on more air conditioners. However, to do this, the fans that are currently running must be stopped, otherwise the airflow in the equipment that is being switched on will cause a backflow, which will prevent starting due to the electrical overcurrents that will be generated.
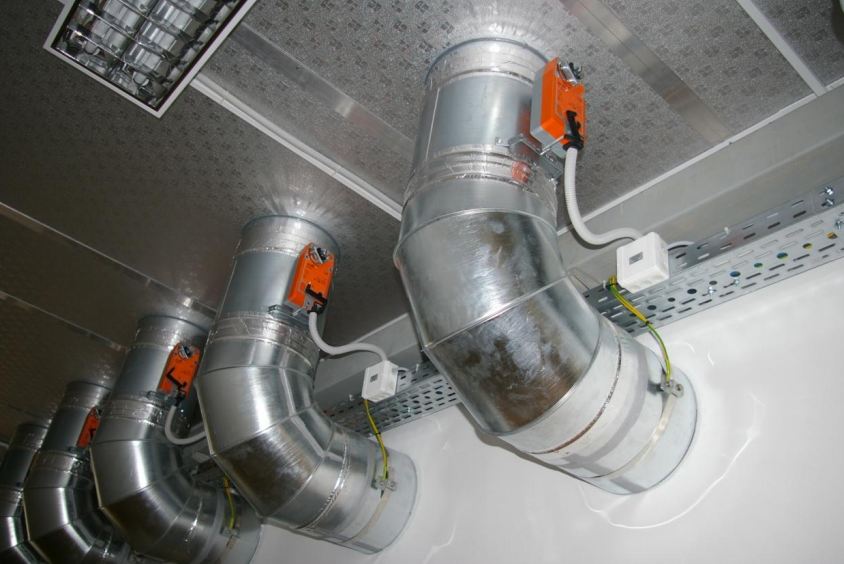
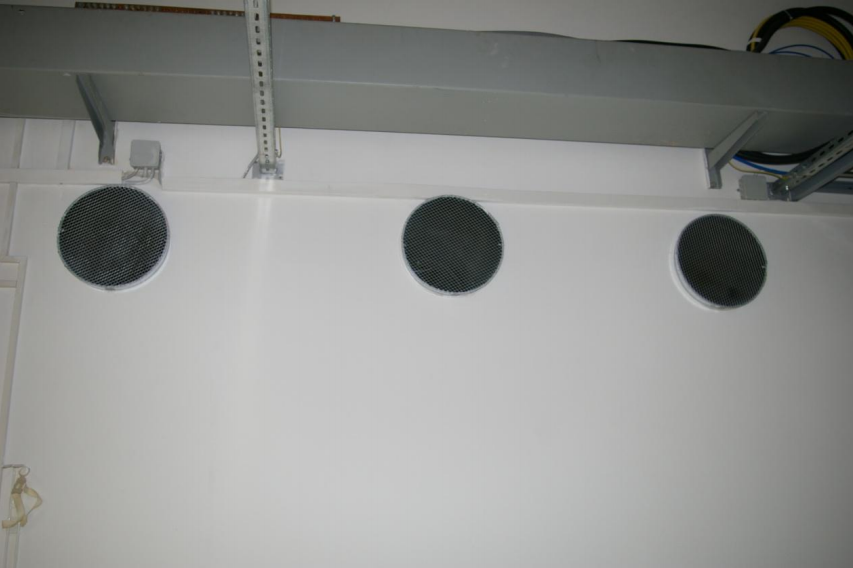
RUBICON control Hardware implementation
Elements of the system:
- 1 RUBICON processor card
- 1 48/12V, 48/5V power supply card
- 3 RUBICON IO cards (2 thermometers, 8 digital inputs and 12 digital outputs)
- 23 12V industrial switch relays
- 1 220/12V power supply to power the relays
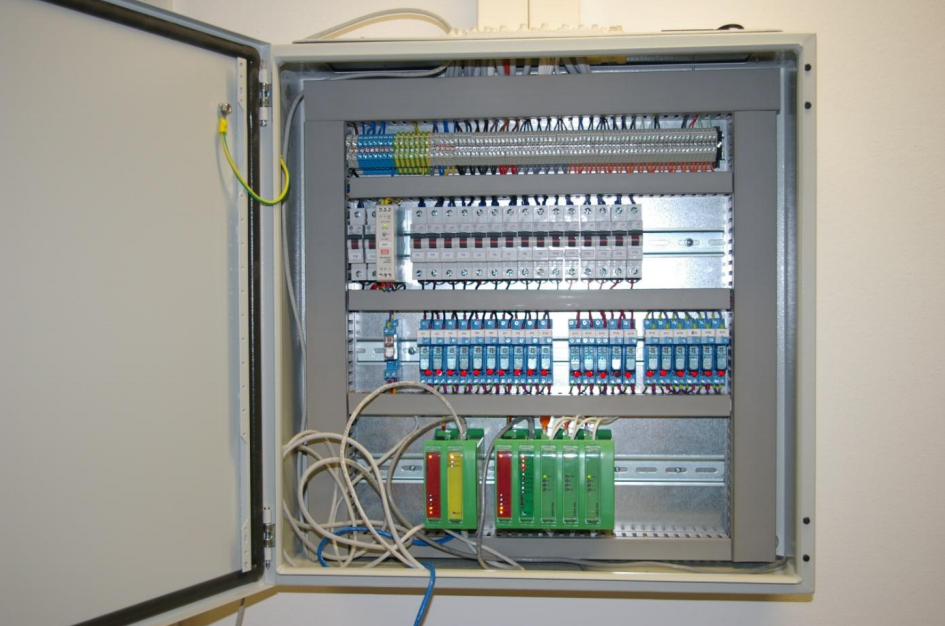
Software implementation
The application (control configuration) running in the RUBICON hardware module was implemented in the RUBICON “RUBICON Designer”, a dedicated application.
For this task, we created several control functions (controls) that can be reused in similar tasks. These elements, as building blocks, can be used to create controls with similar principles but different parameters, for example, for more rooms with fewer air conditioners. The building blocks allow the control of up to 10 rooms and up to 5 air conditioners with up to 5 sets of dampers per room.
The Biatorbágy configuration will control the cooling of 4 rooms with 3 air conditioners and possibly ventilation. Each room has an independent control system to operate the air movement dampers associated with each room. There can be a maximum of 5 of these shutters or groups of shutters. In the rooms, the air temperature must be kept within the so-called “expected temperature limits”, which the system tries to achieve by closing the shutters, and if this fails, a signal is sent to the central control that there is not enough cooling air or too much. A central control algorithm controls the operation of the air conditioners. Decides whether the outside air is suitable for ventilation or not. It monitors the room signals to see if more cooling air is needed or if there is too much, and determines the number of new air conditioners or the number to be shut down accordingly.
The central control is complemented by a separate algorithm that actually controls the corresponding air conditioners. It monitors the running performance of the machines, switching on the ones that are running the least. It coordinates the parallel air conditioner starts and controls the shut-off dampers, i.e. the dampers that prevent the return of air, and the dampers that switch the ventilation/cooling operating mode. The operation is supported by some additional controls.
The temperature averaging algorithm, eliminates the uncertainty arising from the digital processing of thermometer signals. The temperature variation, heat rate calculation algorithm, determines the temperature variation during the given time constant and its trend in °C/min.
The initial parameters are defined by an auxiliary control, a series of power variations of the air conditioners or a series of combinations of the dampers when the system is parameterized at start-up. These sequences allow the central controller to select the switches corresponding to the control levels. This function is activated when an air conditioner enters a so-called disabled state due to a fault or maintenance, in which case the disabled machine is removed from the air conditioner’s power variation sequence and the central control logic no longer expects it to be controllable.
The shutter fault monitoring logic is not directly involved in the control, but it monitors the end position feedback from the shutters and if it does not match the expected (controlled) state, it signals an error, which can be used to restart a machine. And after repeated attempts, you can shut down the system to avoid damage.
Another feature is the monitoring of the closing of the doors of the rooms to be cooled, as the efficiency of ventilation cooling is greatly reduced when the room door is open, so the system automatically switches to active cooling when the door is left open for a longer period of time. As an additional service, the RUBICON controller monitors the fire alarm, which is provided by an external system, because all shutters must be closed and all machines must be shut down.
The status of the system can be checked visually via a WEB interface, and the parameters that determine the system’s operation can be set or changed during operation via a similar simple interface.
Made by Zoltán Ágoston
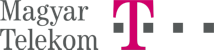
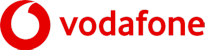